Gates
Radio M-5078 Commercial SW AM/CW
Transmitter
Restoration Details
By John
LeVasseur, W2WDX
Copyright March 05, 2012
Gates Radio M-5078 Commercial SW AM/CW
Transmitter
Restoration Details - Part Six
Transformer Restoration
Continued
Dated: April
17, 2012
It has been a few weeks since I have added anything to this
article. Work has interfered with play, so I haven't been
able to work on the Gates (or this article) as planned. The shop
is full of radios right now; to restore and get sold. So the
benches have been full with no room or time for much else. That
should be a good thing, right? Hmm...
In the process of working on this radio and writing this article
as I proceed, I gave away one of my little trade secrets for
decals, and that's just fine. However, we (my partner and I)
did realize that there may be a need for these decals in the
community. I have scanned so many decals and stickers, for
Collins, Hallicrafters, R390a's, etc. that I have a big
library of reworked images and artwork. So we have decided we are
going to make available for purchase as many of these decals,
labels and stickers as we can. We don't know the cost
structure yet, but we will figure that out soon enough. Also we
are not even sure what decal artwork we have. They will have to
be cataloged, organized and printed. So it will take some time to
have it all ready for market. But I will let ya'll know when
the time comes.
Do any of you have an interest? (message me) I ask because for
the casual home DIY'er the imaging process is painstaking,
the decal sheets are expensive, and the High-Resolution printers
needed to make very high quality printings are also
expensive.
Transformer Housing Stripping &
Repainting
I don't know about you, but I plan on being around at least
another forty years. That being said, when I fully restore
something I want it to look & perform as new and last that
way for decades. Both for myself and my customers. So painting
and the prep work that goes into it are a crucial step.
In Part Five, I showed how I repainted the UTC Modulation
Transformer. It had little rust and was simple to refinish.
However in the case of the HV & Choke iron, significant rust
had formed and this called for a complete chemical stripping and
rust inhibiting treatment. Also I had decided to prime and paint,
instead of simply repainting.
Chemical Stripping
I have not ever been a fan of sitting there for hours and sanding
paint off something. Who is? I have always used chemical
strippers to remove old paint. Any good paint stripper will work.
I am a big fan of Original Rock Miracle Paint and Varnish
Remover. It works great on wood, metal surfaces and strips
varnish, enamel, & lacquer paints in a few minutes. However
you should always keep in mind it does the same to epoxies,
vinyls, phenolics, acrylic, & urethanes, so caution should be
used. I generally only use it on components that have been
completely removed from the chassis and never inside a radio. The
primary active ingredient is Methylene Chloride.
It's simple. In the image below you can see the transformer
housing has had a liberal amount of remover applied onto the
paint. You let it sit for about 20 minutes, then rinse it with
warm water under the tap using a stiff brush. This stripper is
water soluble so it comes off with water along with the old
paint. If after you are done rinsing, and any paint remains,
repeat the procedure and all of the paint will be gone the
second time around. Good stuff!

Rust Treatment
Once again, sanding is required to remove surface rust, and
smooth the surface for painting. Again do not use course grades,
start at 600 and work your way down to finer grades till you see
few surface scratches. Use water when sanding. Wet sanding helps
keeps the sandpaper cool, and carries away the dust so the
sandpaper doesn't bind up.
Once you complete the sanding, treat as mentioned in Part V with
a rust converter. Below is an image of one side of the housing
after stripping and the other after sanding and rust conversion.
The one top is stripped and on the bottom is the finished sanded
and rust converted example.

Priming
One thing I have not mentioned is primer. The UTC transformer was
in pretty good condition so complete stripping and priming was
not important. However, since these housings were in need of
complete refinishing, using primer is a good step to ensure a
long lasting and good looking final finish coat.
For metal painting I always use a Zinc Chromate based primer.
Again PTI makes a very good green Zinc Chromate primer. Again,
completely wipe down the piece with isopropyl alcohol using a
clean cloth until no sanding dust shows up on your cloth. I use
one light coat of primer and let it dry completely, usually for
72 hours or more. Basically until it feels hard. Then I lightly
sand it using the finest grade paper. I wipe down with alcohol
again as before and letting that dry, and then apply another
light coat of primer. Inspect the coat and make sure no
inconsistencies appear in the surface.
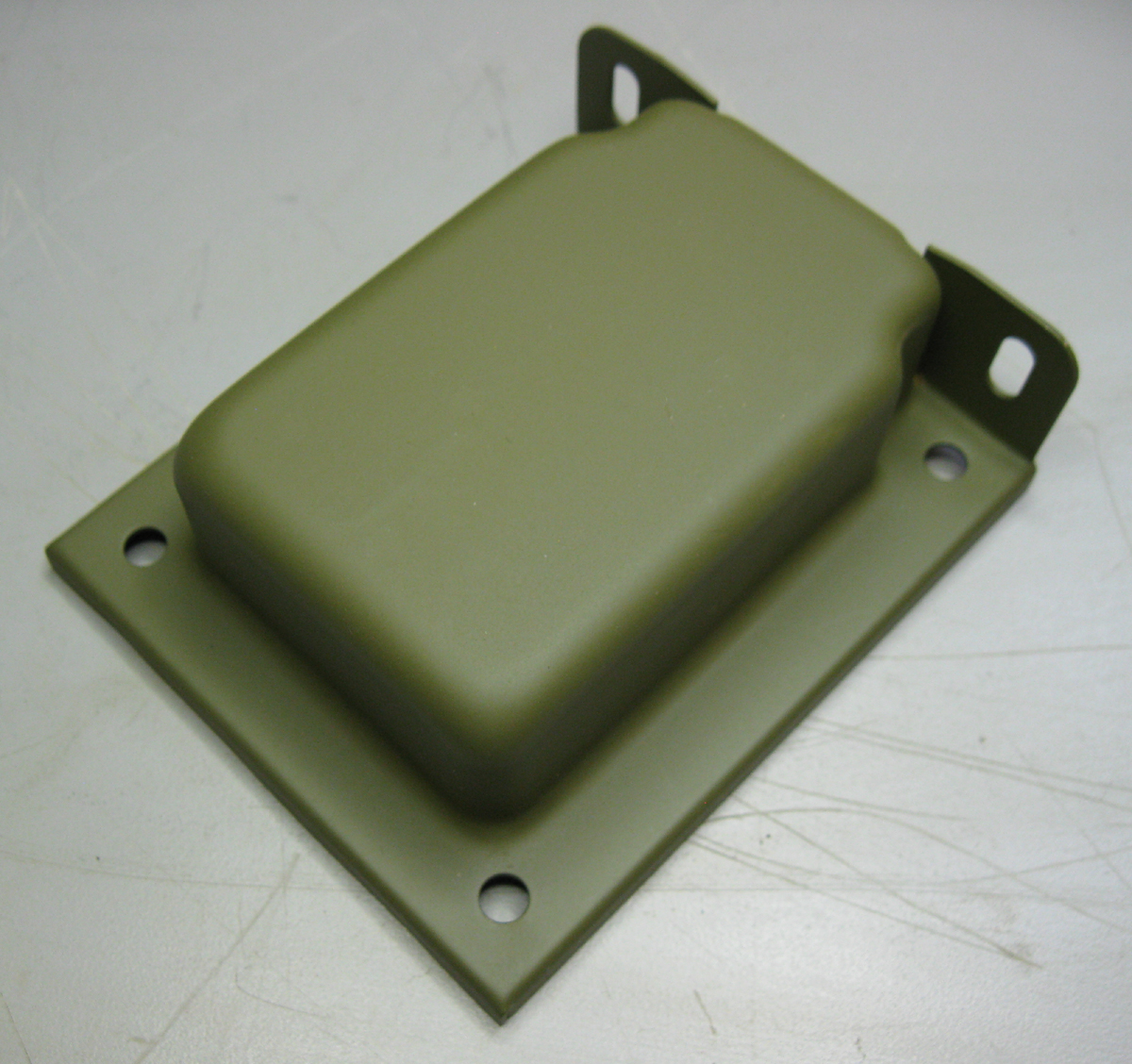
After letting the second primer coat dry completely, wipe down
with alcohol again and apply several light coats of your final
paint. In this case, I used the same PTI Federal Grey I used on
the UTC transformer.
Application of Water-Slide Decals
The Prep
First I should mention that it is very important to make sure the
newly painted surface is fully cured before applying decals. If
you pick up the piece and it still smells like wet paint, it is
still out-gassing the carriers and dryers in the paint. This will
cause bubbles to form under the decals even after they dry, so
patience is key here. I generally will wait a week or more for a
newly painted piece to cure by air, a little less for oven cured
paint, before applying the decals. Don't skip this step! The
adhesive for the decal is gelatin, and it will separate from the
smooth painted surface very easily if the paint is not fully
cured and still out-gassing.
Once you have your decal printed, its time to cut them out. Now
you'd think it's just chop, chop, chop and all done. Of
course not! If you haven't noticed already I have a method
for everything (my partner says I am truly insane in this
respect!) So let me explain the theory.
It is very important to make sure the edges of the decal have no
flaws or micro-tears. The reason is simple. Longevity. Since the
adhesive is gelatin based and water soluble, making sure the
edges of a decal are sealed (more on that later) is important so
as to not let moisture soften the edges of the decal and cause it
to peel prematurely. It also helps prevent cracking and splitting
of the decal when it's being applied and as it dries. Not to
mention the slightest tear in an edge make make the decal split
when you apply it and move it around into position.
So, do not use an x-acto knife or razor to cut out the decal. Use
a very sharp pair of fine scissors and go very slowly. I use a
nice pair of angled fine surgical scissors for this. Works
superbly! Use a magnifying glass if you have one. I have one of
those big ones with the circular light in it. If you were
observant before destroying the original you could see the
original edges. Try to duplicate those, at least for historical
accuracy reasons. You will notice there is a certain amount of
overlap. Leave some of the clear border and do not cut to closely
to the image of the decal.
The important thing to remember is perfect smooth edges, with no
ragged cuts along the edges. So go slow and careful. If you Homer
it (DOH!), that's why you printed several copies of the
decal. Don't use the bad one. Toss it and simply start over
anew.
Dealing with "White"
Now as described earlier, most printers will not print white. And
I am sure many of you do not have an Alps MD-5000 with a white
cartridge. So I have printed these decals with a standard color
laser printer, so that you will see the process for white as you
will most likely experience it. Remember, white will print as
clear on a clear decal sheet.
It is important that the surface be smooth under the decal. Any
defect in the surface under the decal will show as a ripple or
bump in the decal. It may also cause the decal to not adhere
cleanly to the surface; and bubble or crack over time. This is
why you must be very careful in the following step.
Since the lettering on the Triad logo and the lettering on the
specifications decal are to appear white, and since they are
clear on the decal, we must paint the transformer with white
paint ONLY in the places where we will have this
lettering. So we first must figure out exactly where we are going
to place the decal, and where the white underlying paint must be.
The best way to do this is by creating a mask.
You may remember earlier when we described how to print the
decals in Part V, that I suggested after checking the scale of
your decals with plain paper, that I mentioned a
"transparency" sheet. This is a clear sheet of plastic
designed for printing on printers. (Mostly used for presentations
on overhead machines and artwork.) These can be bought at any
office supply retailer. Print out a decal sheet on this
transparency and cut out one of the decals, leaving a lot of
overlap. This is not the actual decal of course so the bigger the
better. This will just be your guide for making and positioning
the mask we will make.
You will need the following:
- Small sheet of wax paper
- Wide masking tape, 2" is
good
- The transparency
- Some newspaper
- A Pin
- Thin light cardboard - like the type on
the back of a note pad
- An extra fine tip marker
- An X-Acto knife (new and sharp blade
please)
- Straight edge
- White spray paint
Boy ... when I write it out like that it seems
like a bit much!
First lay out your wax paper onto the cardboard and tape it down
to the board. Next, take a length of masking tape and lightly
apply it to the wax paper. Carefully overlap several strips if
your decal is wider then the tape. Don't not press the down
onto the wax paper too much, we will be removing it at some
point. However do make sure it is flat with no ripples, folds or
creases. Take your transparency and lay it over the masking tape,
lining it up so that the area where you need white is under a
single strip of tape, if possible. Tape the transparency flat to
the wax paper/tape strips so it stays in place.
Now, take the Pin and locate a solid area of color (other than
the white area) and poke a small hole through the transparency,
the tape, and into the cardboard below. You will see this hole is
chosen to be a point where the mask edge will originate, so chose
a point underneath an area of solid color on the decal adjacent
to where the white is needed. It doesn't need to be a big
honking hole, just enough to insert the fine tip marker through.
Make several other holes to complete a square or triangle or
whatever geometric pattern needed for the white paint. (See
images above and below.)
Once you have made your holes, remove the transparency and put it
aside (we will use it again later.) Now very carefully cut out
the pattern using the holes you made as a guide. If the area that
needs to be white is a triangle you have made three holes one for
each corner, and square you have made four and so on. Line up the
corners with the straight edge and cut the tape along this edge.
Be precise and careful and keep the corners neat!
When you are done, remove the center piece of tape you have cut
out carefully from the wax paper. Leave the rest (the actual
mask) there on the wax paper for now. Take your transparency with
the holes in it and use it on the piece you are applying the
decal to find the right position. Once you have the transparency
"decal" lined up where you want it, tape it down to the
piece. Using the fine tip marker use the holes to make tiny dots
on the object; poking the marker lightly through the holes in the
transparency. These will be you guide marks for placing the mask.
Once the marker has dried, remove the transparency. You do not
need it anymore and it can be tossed. I stuck mine on my cat, for
a giggle!
Now very carefully, making sure not to tear or stretch it, remove
the mask from the wax paper. Carefully line the corners up of the
mask to the dots on the piece and secure the mask to the item.
Firmly smooth the tape down, making sure the edge is smooth. Once
this is done tape some newspaper with some additional tape around
the piece to prevent over-spray of the white paint.
Now spray very light coats of white paint over the mask. A light
coat is very important. We only need it to be white, not be a
coat for protecting the piece. Paint for color, that's
all.
Before the paint dries. carefully remove the making and
newspaper, being VERY CAREFUL not to smear the paint or the edges
of the still wet paint. Let this dry completely for a few
days.
If you were lucky and the paint laid down in fine coat, and the
edges of your mask didn't make a hard seam in the white
paint, you may not have to do much preparation for the decal
other then wiping it down with alcohol. If the edges have ridges
or some other defect at the transition between the white paint
and the bottom paint, you will have to smooth this out so as to
not have ridge line running underneath you decal.
One method is to use a eraser on a pencil dipped in rubbing
compound and very softly rub the edge as to only remove the rough
edge, but not any of the paint. Wipe it off carefully as to not
scratch any of the paint. But get the surface smooth, most
important!
Applying the Decal
Wipe down the area where the decal is to be applied with alcohol.
Make sure the alcohol is dried up before starting to apply the
decal. You can now apply the decal as described in Part V. Just
make sure you line up the decal with your white areas carefully.
As you can see on the right, the vertical line representing the
core does not have the white paint lined up correctly. The gray
paint of the choke is showing. So it is very important to make
sure the white paint is properly applied and the decal aligned
correctly.
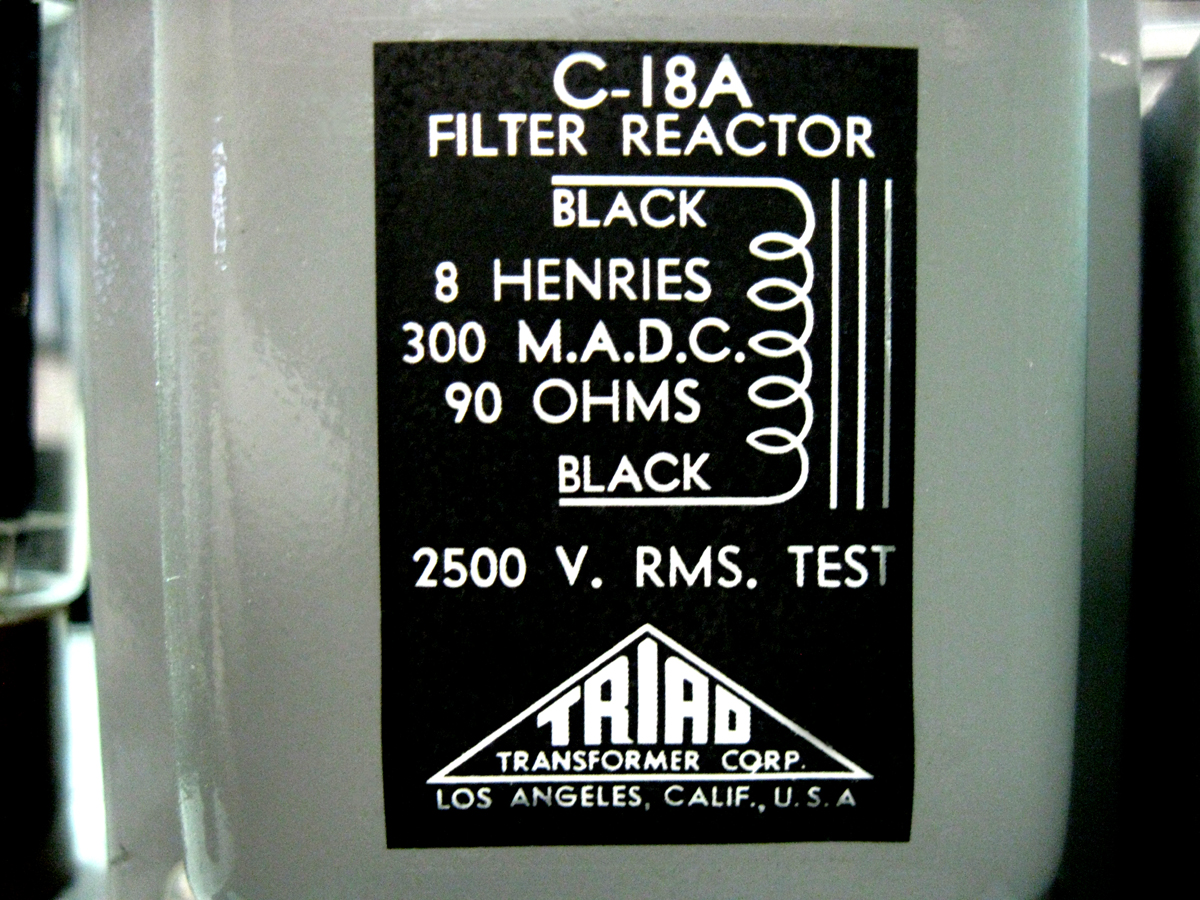
Now that looks just dandy ... eh?
Painting the Laminates
The final step is the painting of the laminates of the
transformers. In this case they are painted a different color
from the housings. Black in this case. The first thing to do is
make sure the transformers are "bound" and sealed
before doing any sanding and painting. By bound I mean securing
the laminates with the screws used to hold the outer housing in
place and keep the laminates tight. However it is important to
not simply put the screws in palce against the laminates
themselves. This may cause the laminates to bow. The housing also
serves to distribute the force of the screws across the length of
the laminates, preventing this bowing. If the laminates separate
much, either from this bowing or from loose screws, the
transformer will hum and buzz.
There are two approaches you can use while prepping and painting
the laminates. The first is to paint the laminates before you
disassemble them with the housings still in place. I don't
recommend this method for one simple reason. If you do have to
sand a little rust off, it could get inside the transformers
windings and have a negative impact on performance or even cause
a short. But many folks do it this way, without incident, or so
they say.
The other method is of course the "hard way", but it
also assures a level of safety. I produce a "O"
shaped (or sometimes a "U" depending on the
transformer) jig made from 1/4" steel stock. I cut it out to
match the shape of the edge of laminates where the housing
normally touches and drill holes for the screws. It's a bit
frustrating for me right now since my little machine shop is not
set up in my shop right now, but instead my milling machines,
lathes, cutters and metal bending equipment is at my residence.
Makes it tough to fit something when the tools are not right at
hand. Grrr... Fortunately, I had two jigs in the shop from
previous transformers that happen to fit these two transformers
from the Gates.
These jigs hold the laminates securely and distributes the forces
evenly across the surface. It gives me full access to the
laminates and also allows me to mask off and seal the rest of the
windings and wiring. I can now sand, and prep the laminates and
paint them in the same tension they will be held at when the
transformer is fully assembled. It also allows the paint when dry
to hold the laminates in place while assembling them and helps
reduce hum and buzzing.
Once this jig is in place the procedure is nearly the same for
prepping and painting as for anything else. Just make sure you
carefully cover (mask) the windings and wires. Below the images
show the transformer with the jig, the prep & masking and the
final painting.
This last image is of the reassembled &
completely restored choke transformer.
Looks as good as NOS!!!
I think its time to draw attention to a few
points on what a full restoration is.
First, it may seem that the methods I describe here are ... well
... driven by some obsessive-compulsion. Not so! Perfection is
not an achievable reality. However, there is something to be said
for details. I have made a philosophical engineering choice. When
you perform a full restoration there should be a minimum
requirement for historical accuracy or at least a level of
accuracy that is achievable with modern equivalents. The
manufacturers strove to make things a certain way, not because
they were perfectionists but because they were striving to make a
quality product. Additionally the nature of the technology at the
time demanded more care for performance, safety &
reliability. In a true restoration, it is smart to do research to
ensure your unit is brought back to its original condition for
the same reasons. Otherwise, you are simply refurbishing
something, not restoring it.
Much of what I have discussed so far has been cosmetic. This is
true. As I said in the beginning, the radio was functional and
the major components checked out as OK. So once the radio is
restored cosmetically and reassembled, we will go through the
process of testing & troubleshooting the electronics and
replacing any faulty components. Then we will align and test the
radio. So all that is coming.
More coming soon!
73'
John LeVaseur. W2WDX
All text and images
contained herein are under strict copyright.
Reprinting or publication in any medium is not allowed without
express written consent of the author.
Copyright 2012 John LeVasseur
|