Gates
Radio M-5078 Commercial SW AM/CW
Transmitter
Restoration Details
By John
LeVasseur, W2WDX
Copyright March 05, 2012
Gates Radio M-5078 Commercial SW AM/CW
Transmitter
Restoration Details - Part Five
Removal &
Restoration of Transformers
Dated:
March 26, 2012
As I had mentioned earlier, we will explore how we removed the
transformers from the chassis. How we prepped and painted them,
and how we restored and recreated the original decals. Not only
does this highlight this particular restoration, but also give
the reader some insight that can be applied to any similar
restoration work.
After inspecting the general condition of the transformers we
decided we would fully refurbish the exteriors of all the
transformers. The transformers passed all electrical tests, so
all that was needed was to remove rust & corrosion, take
steps to inhibit further corrosion, repaint them. In the process
give them that "brand new" look.
- Removing Transformer from
Chassis
Removing transformer can be either simple or
more problematic. The simple one's are when the wiring is
loose and easy to pull through the chassis. The transformer can
be unscrewed and removed with little fuss other than desoldering
and labeling of the wires.
Most transformers that have bell type housings have the
frustrating fact that the wires are fed through holes, and not
slots. This means in order to remove the outer bell housings, you
need to completely remove the transformer from the chassis and
disassemble them.
Another complication comes when the wiring in the chassis is
accomplished with harnesses. The wires are bound together and
held in place with wax covered lacing. This is the case with this
radio.
Below is an image of the modulation transformer as seen from the
bottom, still in place. The wires were first desoldered, then the
nuts and bolts holding the transformer to the chassis are
loosened and removed.
The transformer in this case removes very
easily. It is a good idea, even though the wires stay in place
well to label the wires, in this case with the numbers of the
pins. Once you get the transformer out before you do anything
remove all the old solder from the pins, using a desoldering
iron, an iron and a sucker or solder wick. Do not wire brush!
This can remove the good soldering surface already present and
can send bits of conductive dust into the transformer. Just give
them a good suck! ::)
The next couple of images show the prep and
repainting of the modulation transformer. Special attention
should taken in the preparation of any metal surface paint job.
More time spent in properly preparing the piece to be painted
will mean less paint needed to cover the item. By using light
coats, in two coats, is mostly all that is needed. Additionally,
thinner coats means a smoother finish, with no dripping and less
"orange peel" effect. It also makes a smoother finish
if you need to apply water slide decals (but more on that
later!)
The modulation transformer was in fairly good relative condition
compared to the others. So we opted a basic approach to prep. We
first used 400 grit sandpaper to remove the rust and pitting,
being very careful to avoid the aluminum plaque/label. You do
want to run sandpaper over this. It will take the printing right
off and take away any brushed aluminum look it may have. Avoid at
all costs. We will deal with this separately with a different
method. The two images below show the transformer and its label
in their original state.
At this point it is good idea to convert some
of the rust on the bare metal surfaces. Take a small amount of a
good rust inhibitor like Eastwood Rust Converter and wipe only
onto the bare metal that is exposed. You do not nor should you
coat the entire surface where old paint remains. Only touch up
the areas where you sanded away rust spots and pitting. Use only
something called a rust "converter". Once this dries,
and please do wait for it to dry completely, continue on with the
sanding.
Once you have removed and converted the rust and pitting and
smoothed out the old finish, it's time to remove the
scratches from the heavy sandpaper. Use progressively finer grit
sandpaper down to at least 800. When you are down to the finer
grit, use water as a lubricant/coolant. The old paint will soften
from the frictional heat of the sandpaper and either ball up or
tear. This will create a lumpy surface when you paint. So use
waterproof wet sandpapers, use them with water, and do not rub
hard. Just smooth it softly and let the paper do the work. Wipe
off the work with a clean rag occasionally looking at the finish.
I cannot emphasize any stronger how important the technique in
this last paragraph makes a difference on the final finish.
Once you are satisfied the surface is perfectly smooth, wipe the
complete surface down with damp paper towels until you no longer
see any dust on a clean damp towel. Now lets move onto the
label.
Label Before
Prep
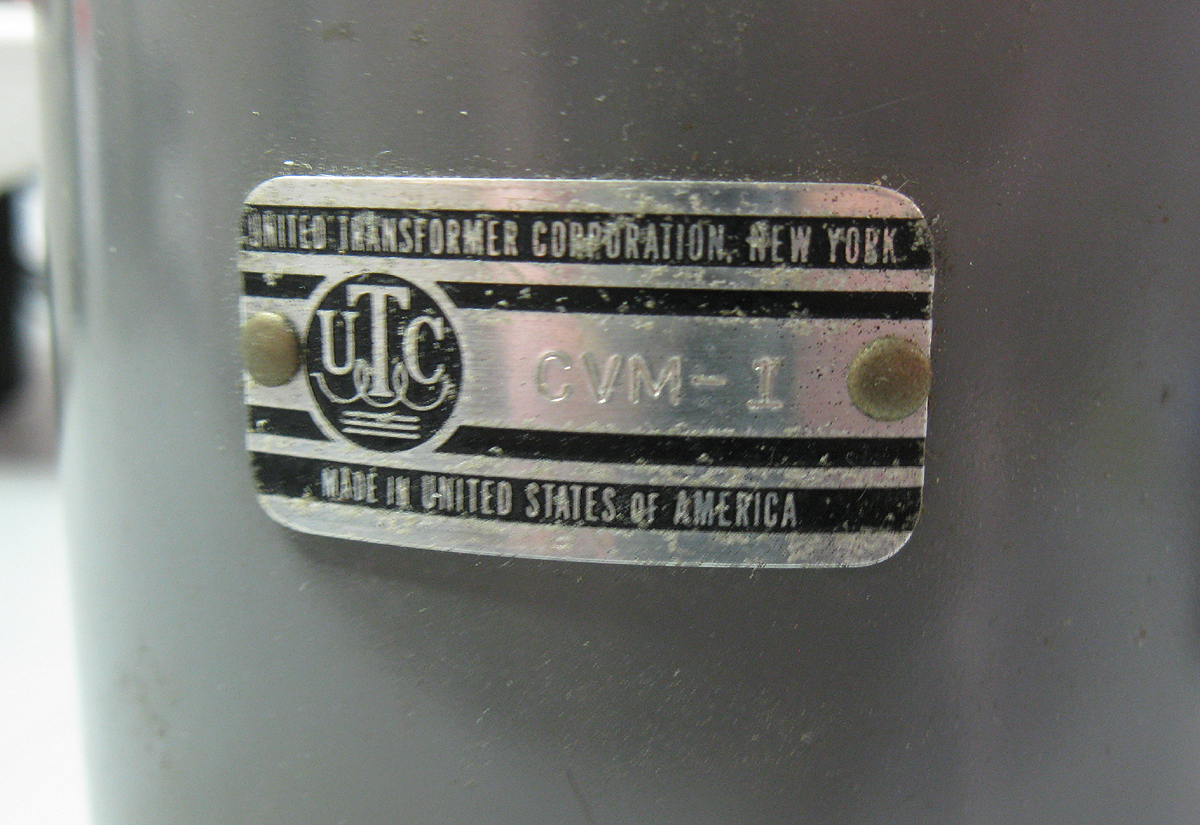
Since this particular transformer is a seal
"potted" type, it is not recommended to take it apart
to remove the label, polish it and reinstall new rivets. So we
have to prep it in place. With these labels you can use a small
paper towel with a little bit of white compounding paste. Make
sure you rub in the direction of the brushed aluminum. Also use a
small amount of compound on a small piece of cloth, no bigger
than the label. You want to avoid from getting compound waxes on
the surface you will be painting later. As with the front panel
buffing earlier it is important to pay great attention to the
printing and to not rub too hard to wipe it out of existence.
Only slight pressure is needed. This process will buff up the
aluminum, make the printing blacker and remove any oxidation.
Once you are happy with the label, you will need to mask it off.
On smaller pieces like this I like to use brown shipping tape.
Masking tape will work, but you need to make small bends and
tight fitting to cover these types of labels and regular masking
tape is too "bulky" for this work. Place a piece of
this tape over the label and carefully trim it close leaving a
tiny strip around the edge to fold over and cover the edge as
well. Using a razor (lightly to the extreme) will accomplish
this. Below is an image of the tape (and a mistake which we will
highlight later.)
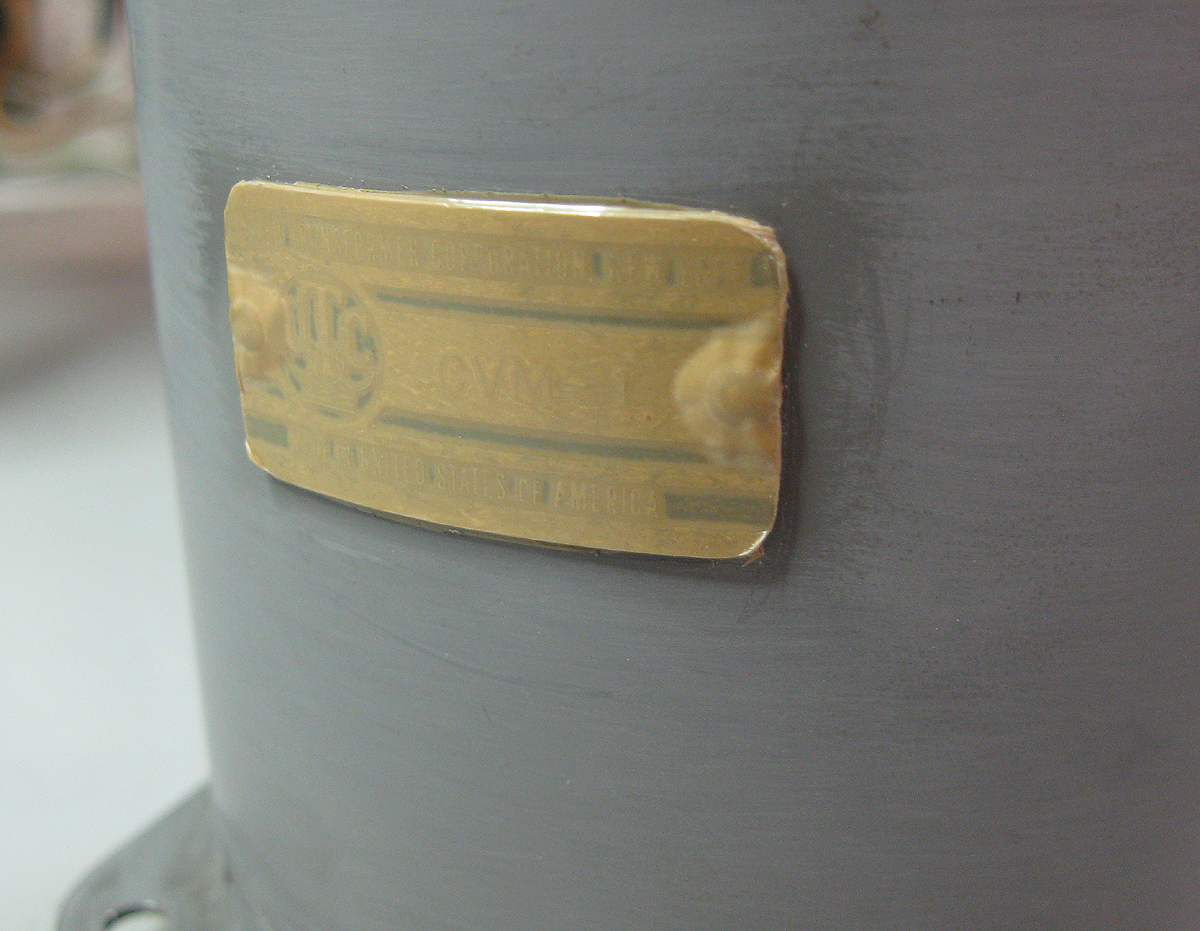
If you look closely at the top & bottom
edges you will see a small strip of tape that did not tuck under
the edge of the label. Avoid this and make sure that either it
gets tucked under or is trimmed clean. You can see the right side
where the tape is properly masking the edges. This oversight, due
to old eyes, lead to an obvious seam in the paint just above and
below the label. And a real nuisance it is to correct later.
It's like they say (whoever "they" are), it's
all in the details! (I did correct this later, because I am just
that persnickety.)
After you're done with your masking, it's time to give
the item its final wipe down. For this you use a high purity
isopropyl-alcohol (91% or higher.) Lightly dampen a very clean
cloth, and wipe the entire surface again, looking for dust.
Repeat until you see no more dust on a clean alcohol cloth. Be
careful to use the alcohol sparingly, since you want to avoid
loosening the tape on the label.
Your transformer is now ready for paint.
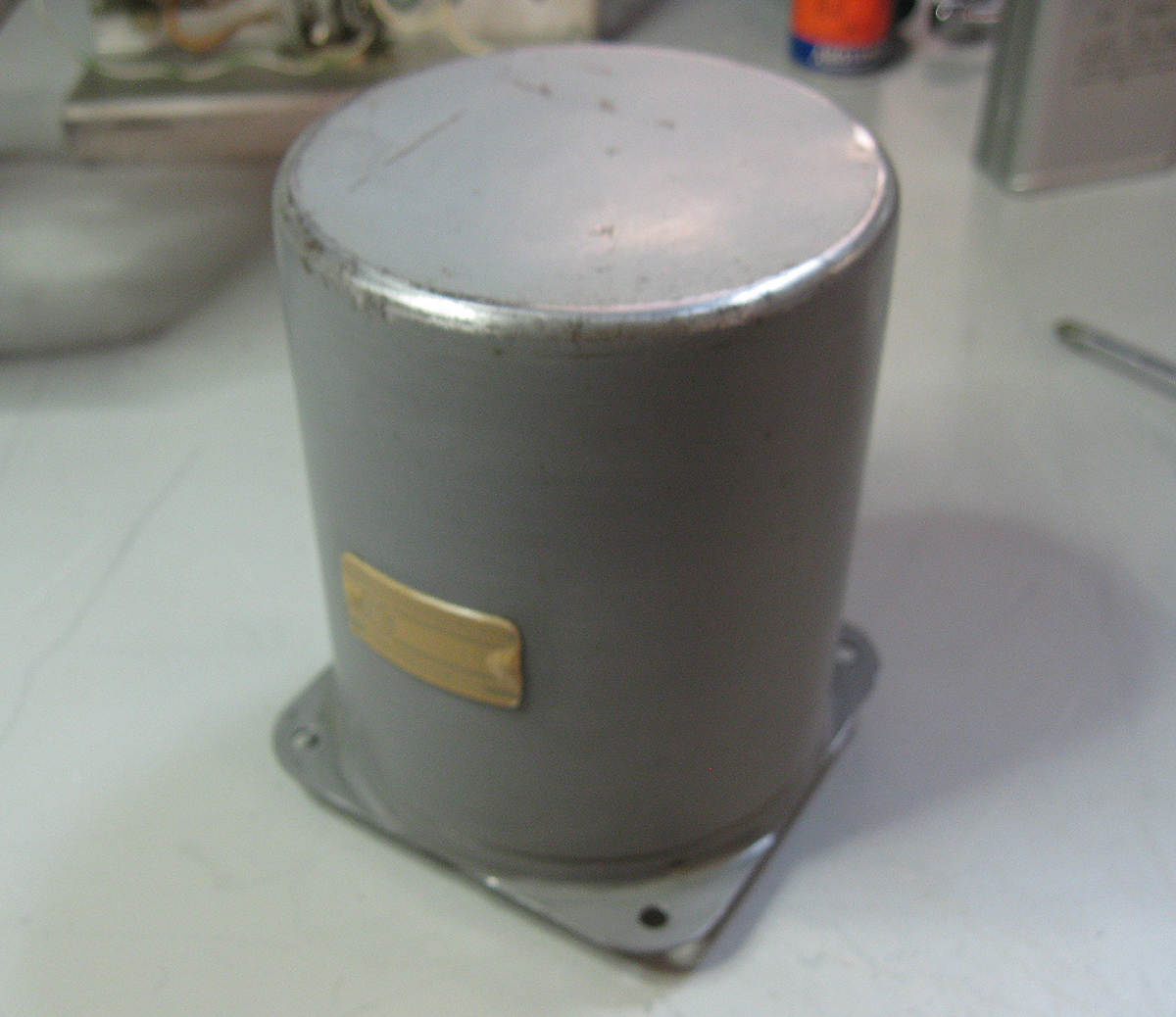
- General Information about
Paint
Paint is a subject that has received a great
deal of attention online. There are many types of paint
available, designed for many uses. But as you have seen earlier,
I like research. So, here's a couple of good tid-bits I have
gleaned over the years.
Spray Paint
There is a literal plethora of spray paints out there. Most are
crap, plain and simple. Krylon is great if you have stuff around
the house that needs color. With Krylon and other consumer levels
paints, it's all about the color and not about things like
surface hardening & scratch resistance, gloss, or even
consistency of finish.
Krylon is a fast drying paint. As a result it equates in the same
way epoxy does. Fast curing, softer weaker epoxy. Slow curing,
harder & stronger epoxy. Paint is same way. If is says
"fast drying", I say "later"! The idea is if
a home owner paints his table legs blue and they get scratched or
chipped, he'll just take more spray paint and cover it. The
initial finish hardness is not a priority when companies
formulate paints for this market. Also the paint is soft in
hardness to allow better adhesion of repainting. On smooth metal
surfaces that are seen in close proximity, every detail in the
paint surface is clearly evident. Also it is amazing how handling
a piece will lead to fine scratches, especially on faceplates
around knobs. Krylon and many consumer grade paints just
aren't up to the task.
Good industrial paints made for prepared metal surfaces are
always preferred, yet before the internet were harder to find.
And yes they are more expensive. However, due to fact you have
prepped your piece properly, and because industrial paints have a
better "lay", you may actually use less over time. A
brand I recommend is from a company called PTI (Products
Techniques Inc.) In this case I used ENA213a Federal Gray Enamel
Spray Paint. "Federal Grey" is a general US government
standard specified color usually applied to most items used for
military or government contracts. It was commonly used for many
parts and components and faceplates for many communications
equipment sold to the military. It was also used quite a lot in
commercial products. My preference for PTI is that I have
experience with it from the audio and satellite communications
companies I have worked for over the years.
However during my research for this particular radio I discovered
PTI was and still is a vendor to Gates and now Harris. According
to PTI they also provided paints for Continental and Raytheon for
a variety of products. You can also include Hammarlund,
Hallicrafters, and Teledyne. They are also a big suppliers to the
aerospace/aircraft industries.
My source for this, is again the general aviation supply
industry, so try that online. Again I like Aircraft Spruce.
Applying Spray
Paint
Once you have properly prepped your piece, it's time to apply
your paint. A clean dust free environment is again crucial in
making sure your finish come out smooth and pristine. A proper
painting booth is ideal, but I understand what it is like in a
home. We have a booth here, but let's not go there. Instead
lets just say a cover over your work is one important tool.
Gravity has funny way of focusing itself on your newly painted
item, and forces all the dust and hairs right onto your paint.
(This may be in some way related to birds and newly washed cars.)
So a nice simple device is a clean cardboard box, laid on its
side. Make sure you get all the bits of dust, pieces of paper and
fibers out from inside your box every time you use it. One way to
insure this is to spray the interior of the box with a clear
spray paint in advance. This stabilizes any surface fibers and
bits of paper. Then each time you use your little
"booth" blow it out with compressed air.
Do the painting indoors if you can (with good ventilation.) Make
sure the temperature is proper according to the ranges shown on
the can. Place your item in the box and then leave for a
while. Let the air settle. Come back later and move slowly into
the room. Now you can paint without much worry about dust
settling. Now unless you have a professional high-tech spray
booth with an expensive air handling & filtration system, you
will always get some dust on your work. Even we do. ($25K for the
booth I really want ... ACK!) So just be clean and smart and this
should minimize the dust you do get.
Spraying is important in its consistency and it's
"weight". Weight is how much paint you apply in one
pass. Even short strikes, moving your hand first, then pushing
the button and releasing before stopping the movement. If you do
not cover completely on that first pass, that is fine. Do not
spray the same spot twice. The next few coats will cover that.
The important thing is to apply as thin of a complete coat of
paint as possible on each subsequent coat.
You can either apply the second coat a short time after or wait
till paint fully cures, and apply the next coat. Follow the
directions on the can in this respect. I prefer the latter, since
this give the best hardened surface and the best finish.
Another good thing is to have is a turntable of some kind. I use
one designed for pivoting small televisions. It's heavy
enough and large enough for most heavy small items like
transformers. This way you can turn the piece without touching
it. On transformers two to three coats is plenty. I do not bake
transformers as a rule.
Below you can see the completed Modulation Transformer and a
close up of the label. (Note the bad paint edge on the top &
bottom edges of the label due to the poor masking.)
The B+ transformer and choke were not in as
good as condition as the UTC Mod Iron. They showed much rust and
surface pitting. So instead of repeating anything from above I
will only touch upon what we haven't written about already.
Whew!
Triad during certain years and with certain contracts used Water
Slide Decals for marking and labeling its transformers. Many
boatanchors also have slide decals on various parts and
locations. Now we know repainting is not that big a deal, and we
also love the way a newly repainted radio looks. However there is
always something glaringly missing when the decals are gone
forever. So before we do any prep work on these Traid
transformers we document the decals, in very precise ways.
Below is the choke transformer shown removed from the chassis and
taken apart.
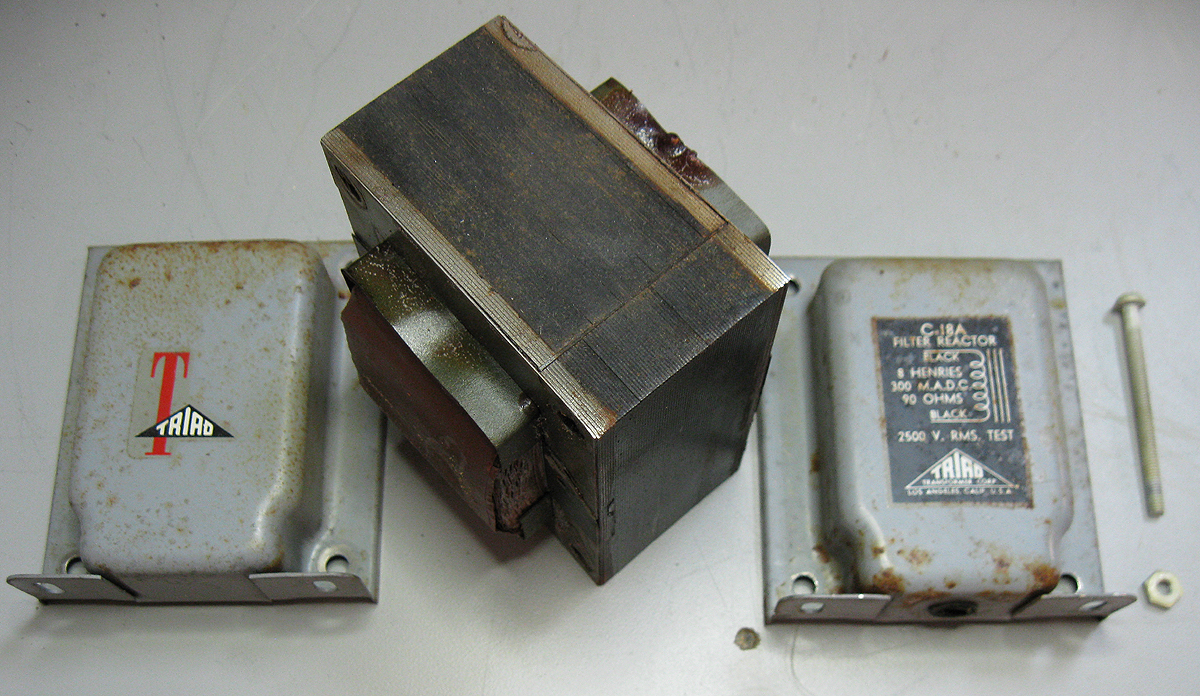
As you can see there are decals on the front
and back housings. Before we do anything we need to get accurate
images or scans of these decals. After that we will take these
scans and convert them back into artwork to reproduce real Water
Slide Decals. The best part it can be done all at home using a
camera or scanner, special paper and your color printer. Hmm ...
Do tell!
The Water Slide Decal has been around for years. It has fallen
out of favor in manufacturing since printed labels or laser
etching can be applied easier to products in our hands-off
mechanized manufacturing processes we use today. Basically, a
decal is a clear substrate with an image printed onto it. This
substrate is bonded to a paper backing with a water soluble
substance. The substrate is clear and was originally made from
gum, which is why they were so fragile. We all had those models
at home when we were kids that had the decal of the Iron Cross or
Air Force Star which was kinda wrinkled and split because we let
the decal sit in the water to long and it torn in half or turned
to goo. GRRRRR ...
Today, you can get very fine thin vinyl or acetate as the
substrate. And they can be printed either on a color laser or
even inkjet printer. More on that later ...
Preparing your Artwork
Let's get going on the artwork to make the new decals. The
key work here is resolution!!! As much as you computer can handle
and as much as your printer can print. Now some wold think well
my printer only has resolution of 600dpi, so I will take all the
images/scans at that resolution. BONG! Nope. Printing images and
digitally processing images are two different things. They
require different levels of resolution & sizing. Now, the
better your software, better you final product will come out. I
use Adobe Photoshop. I use an old version 7 one. You can get this
for free. Do not try to do this in WindowsPaint or some cheesy
software like this. You will not be able to do what needs to be
done in those kid oriented products. Any good image handling
software is good like Adobe Illustrator, Macromedia Freehand,
Deneba Canvas, or CorelDRAW and others.
In the case of the Triad logo we tried using a digital camera set
for Macro (close-up) settings. You zoom out all the way and get
real close. Here's the image of the logo. (this image is
scaled down from the original image size.)
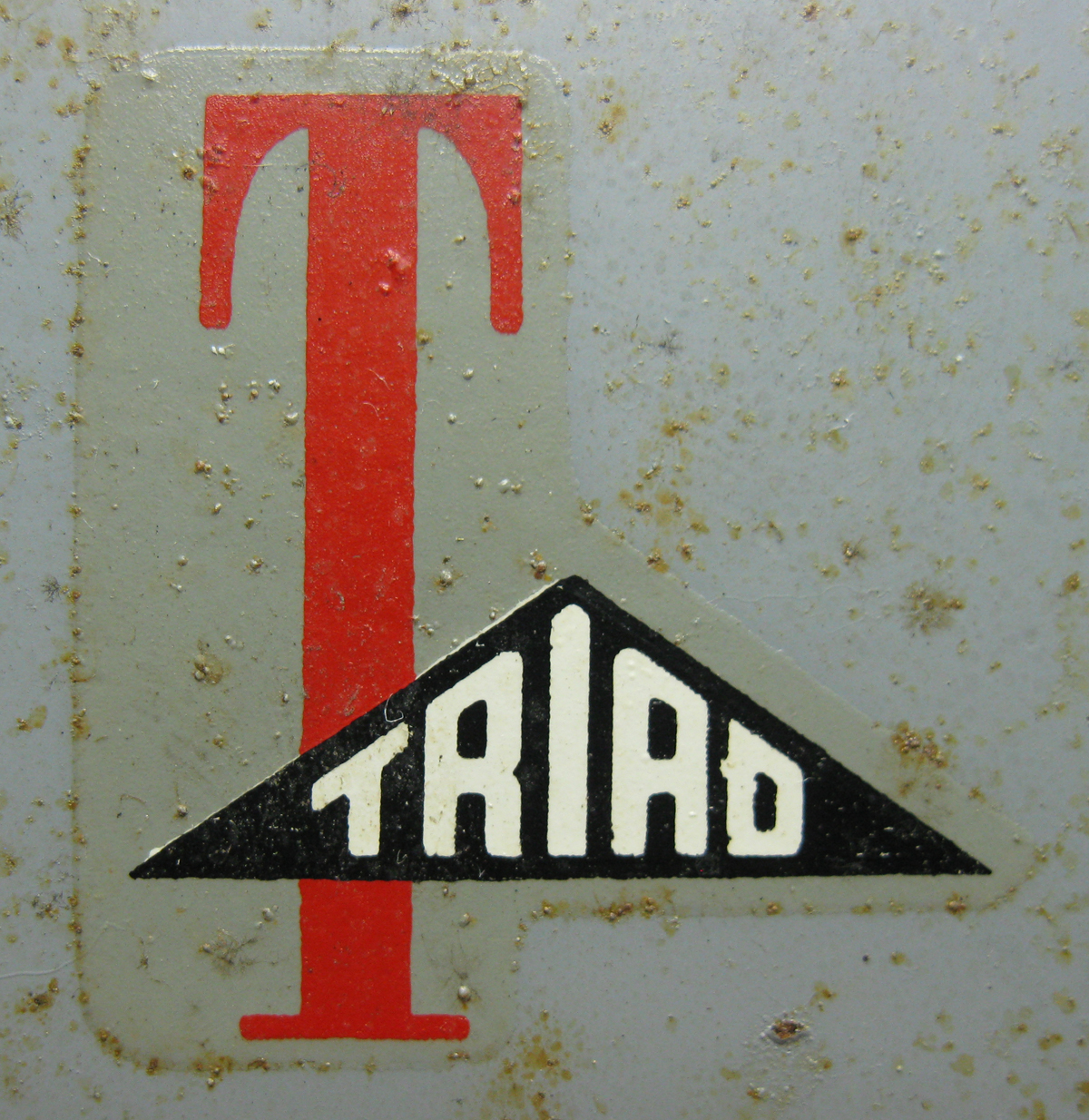
A few things to note here. Set your camera to
its highest resolution. Use no flash. Light the item well and use
the correct color correction in the camera. If you use florescent
light, set the camera for this, incandescent use that setting. It
is very important if you want the colors to be correct. Do not
skip these steps.
One other aspect of using a camera for this is the issue of
parallax. Sometimes depending on the lens and depth of field of
the settings of the camera a fish-eye effect can occur. This will
look like the outer edges are bulging outward. For instance, on a
rectangular label with straight edges the outer edges will no
longer be straight but bulging out in the middle. If this occurs,
you should use a scanner instead. A scanner will make the image
linear in its capture without any depth of field. This will yield
straight edges. In this case, the logo taken with camera
was OK, since it did not have straight edges on the extreme
outside of the image. However, the specification decal, which was
a rectangular box, did experience this problem and had to be
scanned.
Also do not use an image that is even slightly out of focus, you
will regret this when processing the image. Shoot another image
till its perfectly sharp. You can forget about nice sharp edges
if you don't. Once you get the image into your software do
not use "sharpening". This will add pixels at the edges
that will be hard to process. Just have perfectly focused focused
image first. I will show the final image now so we will have a
point of comparison.
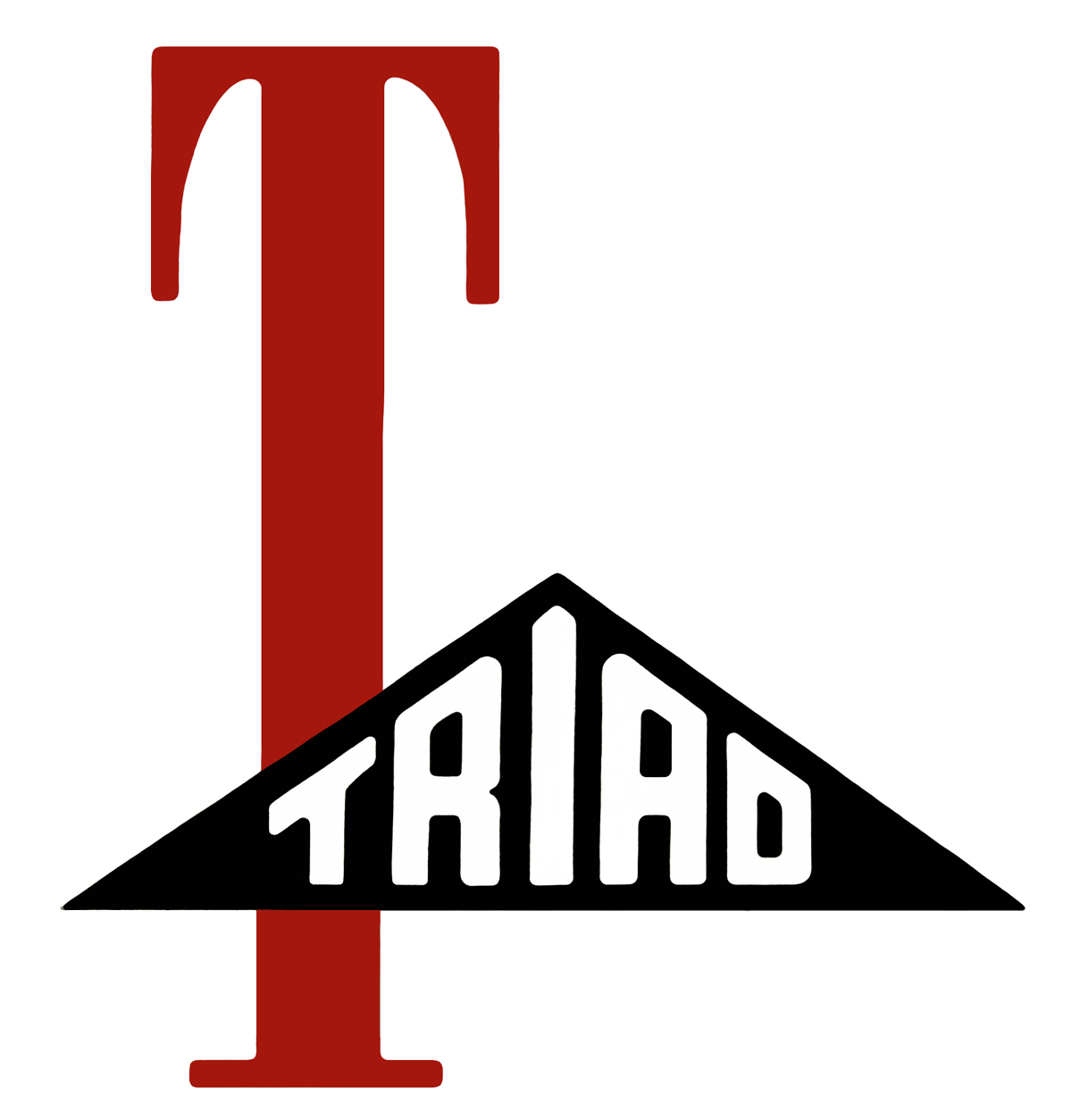
Since I used Photoshop I will be specific
about what I did here. First the original image was opened in
PhotoShop (PS). Next I opened the image size menu and changed the
resolution from 600dpi to 2400dpi. This created a huge image file
that was over 500Mb in size. I "saved as" and named the
file. Next comes the tedious part. I zoomed into the image and
went to the black area. I made a solid black square in the middle
of one of the black areas. From that I used the clone tool and
copied in the areas that were black, using different size tools
and brushes, at times working with brush sizes as small as three
pixels. I repeat the same process with every section. The red
areas I first used the smudge tool to smooth out one area of red.
Like a painter mixing colors on a palette. From this I derived
the red color which I used the eyedropper tool and filled in the
red "T" area.
This also included the "white" area that spells Triad.
Outside of the logo itself, I had to remove all the white and
make the image transparent in these areas. Otherwise when printed
on the particular printer I use the area will print as white. The
Alps printer I use has white ink. If you use a normal color
inkjet or laser printer, you do not have to delete the white
outside, but you do have to still replace the white areas with
white fill, so as to not have the image of the rusty bumpy pitted
transformer image in the lettering. The point is you want to
replace all aspects of the original image with solid true colors,
using the original only as a template to draw over. You only have
to consider your printer type, and then choose either solid
colors or transparency.
I should point out here that I have a printer that prints the
color white. I use an Alps MD-5000. The Alps printer is a
high-res 2400dpi Thermal printer that can print in standard CMYK
colors plus black, white, gold and silver and other cartridges. I
bought this for the sole purpose of creating decals. Sometimes
decals use white on items where the background is black or dark
(or in this case gray.) White will print as clear on normal color
inkjet or laser printers which assume most printing is done on
white paper. Some of the decals I have come across (like on
guitars) also use metallic gold & silver which I can
reproduce in the Alps. So if you have a regular printer but want
the white when you use these decals on dark surfaces, you have to
physically paint the surface white in the right spots before
applying the decal to it. Bear this in mind.
The Decal
Paper
The paper used for this is available from a variety of sources.
If you do not have a printer that can print white you can get the
standard decal paper. If you can print white they make one with a
blue background that lets you see the printed white color. Buy
the thinnest decal substrate they offer. This is more like the
original decal materials available in the 1950's.
There are various sources online where you can purchase this
paper. You may also find it at various hobby shops, particularly
those who cater to model builders. Believe it or not you can do a
search for "Mug Decals" and find a bunch. The thing is
make sure you buy decal paper for your particular type of
printer, inkjet, laser or Alps.
Take this final images and copy it and paste multiple copies onto
one image, or what is called step & repeat. This is shown in
the image below. It is a good idea to make a single image with
its size set to 11.5"w x 8.5"h with resolution set to
the maximum your printer will produce.
This image is a .gif
image with transparency and "white".
How
to print:
- Begin by printing your image(s) from your
computer onto your laser printer, color copier or ALPS printer
with using blank laser printer paper.
- Check the scale of your decals once you
print a sample to make sure they are of the original
size.
- If you have a clear transparency product
this is better for checking the final print quality, but is not
necessary.
- Print on the glossy side of the blank
paper. Note: You should feed your printer one sheet at a time to
avoid jamming the printer since this paper is thicker than
regular paper. If you take it to a copy center, instruct the
operator to feed the copier one by one the sheets into the copy
machine.
- Allow the ink to dry and set into the
paper for at least five minutes and it should be ready for
application.
- Cut out the image(s) as close as possible
to the actual design. I like to try and use the original cutout
outline for these type projects. Place them in lukewarm water for
approximately 30 seconds. Hold the decal carefully to avoid
tearing. You will begin to feel the printed image start to slide
off the white backing paper. This means it is ready to apply onto
your surface to decorate.
- Gently slide the decal into place. Use a
clean damp cloth or paper towel to wipe off excess water and
remove any air bubbles that may appear. Allow setting time of
about 3 hours. Your decorated object is ready! Note: You can
speed up drying time by placing your decorated object under/near
a fan.
- If you wish to protect your decorated item
from surface scratches, moisture, or fading then spray your dried
decorated surface with a Clear finishing spray. I do recommend
you use the spray that is sold with the particular brand of decal
sheet you buy.
One supplier I do recommend is Papilio
(http://www.texascraft.com/hps/home.php). They have a good
selection of types, have one the thinnest varieties available and
offer reasonable priced complete starter or sample kits that even
contain the finishing sprays.
So what about the very rusted transformers
and their repainting ...
The paint had not fully hardened at the time I wrote this
section. Preparing the decal artwork would be the first step
anyway. A more thorough prep was needed on these transformers,
which included chemical stripping of the old paint, heavier
sanding and rust conversion. We will cover that, and the decal
application in more detail in Part Six.
Once the paint dries on the transformers I will post images of
the finished transformers and I might even make a little video
showing the printing, cutting and application of the decals ...
But don't get your hopes up.
Stay Tuned.
73'
John LeVasseur, W2WDX
All text and images
contained herein are under strict copyright.
Reprinting or publication in any medium is not allowed without
express written consent of the author.
Copyright 2012 John LeVasseur
|